The bodywork is under way.
The first step was to set the body on the truck and look at what was going to look the best for the overall project.
First I marked up the fenders with my ideas of how things should fit and look.
Then I dropped off the body to the masters of bodywork.
DSCN3784.JPG DSCN3778.JPG DSCN3783.JPG
Ben is the man that is working as my sculptor. He normally does high detail, dental work for bodywork. He is also an off road guy at hart.
DSCN3794.JPG 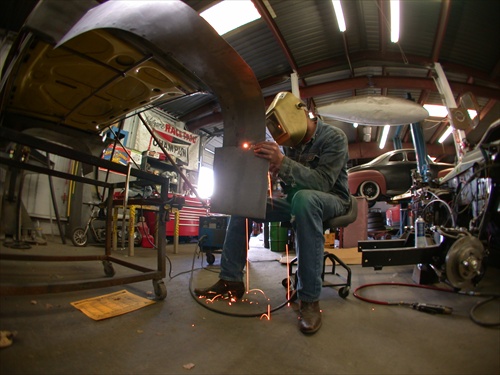
He has wanted to build a truck like mine for years, so he was extremely excited to get the chance to sculpt out the body and pound out some fenders.
He was going to build everything out of sheet metal, but that turned into a problem.
The extreme angles needed to make the body look right made the use of all metal nearly impossible.
So he is going to be using a mix of sheet metal and expanding hard foam to build the fiberglass mold.
DSCN3798.JPG DSCN3787.JPG
The first thing I had them do was shorten the bedsides by 1 foot off the rear, no need for long bedsides.
From there they have a free license to make the front end look correct.
The front end will be widened by 20 inches with tire bumps and flairs. There will be a cowl induction hood designee built into it for clearance of the air intake system. The hood and fenders are going to be a 1-peace designee, with some small fenders, or splash grads. I will update things as we go.
DSCN3797.JPG
Bookmarks